Output
1
Display
|
Action |
Response |
|
Press
MENU
Press ENTER |
1)
Press MENU, if
necessary, until
"out" display
appears.
2) Display
advances to "Self"
submenu. |
SELF
SUBMENU:
The Self option
allows the output
of the controller
to be controlled
manually from
the front panel. |
|
Press MAX
Press ENTER
|
3) Display
flashes the current
setting of Self,
enabled or disabled.
4) Press
the MAX button
to select between
Enable and Disable.
5) If
Self enable was
selected, Output
1 setting is
completed and
the display advances
to the next menu.
6) Display
advances to the
ôMinimum/Percent
Lowö submenu,
if self is disabled.
|
NOTE:
The output is
now under the
direct control
of the operator
and can be adjusted
in the run mode,
by pressing the
MAX and MIN buttons.
The control value
(0 - 99), now
display in the
SV window indicate,
approximately
in percent, the
output. For example,
a setting of
0050 of an analog
output of 0~10Vdc
would produce
roughly 5Vdc
at the output.
Also, to insure
smooth transition
when switching
to self mode,
the proportional
control output
is left in its
last value, when
self mode is
activated for
the first time.
|
MINIMUM/PERCENT
LOW SUBMENU
Specify in percent,
the minimum value
(0000) for control
output. If the
output is analog,
then the minimum
voltage or current,
in percent, is
specified. If
the output is
time proportional,
then the minimum
duty-cycle, in
percent, is specified |
|
Press MIN/MAX
Press ENTER
|
7) Display
shows ôLOö, and
flashes the 10s
digit of the
current ôPercent
Lowö setting.
8) Use
MAX & MIN buttons
to enter a new
value for ôPercent
Lowö.
9) Press
ENTER to store
the current setting
and to advance
to Maximum/Percent
High.
|
MAXIMUM/PERCENT
HIGH SUBMENU:
Specify in percent,
the maximum value
( 0099 ) for
control output.
If the output
is analog, then
the maximum voltage
or current, in
percent, is specified.
If the output
is time proportional,
then the maximum
duty-cycle, in
percent, is specified. |
|
Press
MIN/MAX
Press ENTER |
10)
Display show
"HI"
and flashes the
10s digit of
the current Percent
Low setting.
11) Use
MAX & MIN buttons
to enter a new
value for Percent
Low.
12) Press
ENTER to store
the current setting
and to advance
to *Control Type
submenu. |
Example:
On an analog
output of 0~10Vdc,
a setting of
%LO = 10 and
%HI = 90, cause
the minimum on
the control output
to be 1V and
the maximum on
the control output
to 9V. The same
setting on a
time proportional
output, will
cause 10% duty
cycle for the
minimum control
output and 90%
duty cycle for
maximum control
output. To disable
%LO/HI, set LO
to 00 and HI
to 99. If %LO/HI
is at other values
than the default
(%LO=00, %HI=99),
ôsoakö is disabled. |
|
Press ENTER
Press MAX
|
*CONTROL
TYPE SUBMENU:
(Relay, SSR or
Pulse Option)
13) Display
flashes "on.
oF" or "PId".
14) Scroll
through the available
selections: ON/OFF
or PID. If ON/OFF
is selected proceed
to section Ramp
& Soak |
|
Press ENTER
|
15)
Display flashes
"strd" message
and advances
to "Action Type"
submenu. |
Note: The ON/OFF
control is a coarse
way of controlling
the process. The "Dead
Band" improves the
cycling associated
with the On/Off control.
The PID control
is best for processes
where the set point
is continuously changing
and/or a tight control
of the process variable
is required. PID control
requires tuning and
adjustment of the "Proportional",
"Integral or Reset"
and "Derivative or
Rate" terms by a trial-and-error
method. The Controller
provides an "Auto Tuning"
feature making the
tuning process automatic,
possibly optimum.
|
*If
Current/Voltage
is your analog
control output
1, this menu
i.e. ctrL type
will not appear,
instead 4-20
/ Curr or 0-20/Curr
will be displayed.
Select "Enbl"
for a 4-20mA
output or "dsbl"
for a 0-20 mA
output. If 4-20mA
is enabled, %HI/LO
setting will
have no effect.
NOTE:
Both Current
and Voltage control
outputs are active
simultaneously.
|
|
Press MAX
Press
ENTER |
ACTION
TYPE SUBMENU:
16) Display
flashes "drct"
or "rvrs".
17) Scroll
through the available
selections: Direct
or Reverse.
18) Display
flashes "strd"
message and advances
to "Auto PID"
submenu.
If "ON/OFF"
was selected
in the Control
Type, the display
skips to the
"Dead Band" submenu.
|
Note: The error
that results from the
measurement of the
process variable may
be positive or negative
since it may be greater
or smaller than the
set point. If a positive
error should cause
the controller output
to increase (i.e. cooling),
it would be called
Direct Acting.
If a negative error
should cause the output
to decrease (i.e. heating),
it would be called
Reverse Acting.
|
Press
ENTER
Press MAX
Press ENTER
|
AUTO
TUNE PID SUBMENU:
19) Display
flashes "enbl"
or "dsbl".
20) Scroll
through the available
selections: Enable
or Disable.
21) Display
flashes "stored"
message and advances
to "Adaptive
Control" submenu.
|
If
"Enabled",
the controller
can determine,
by enabling Start
PID, the optimum
values for the
three adjustments
ù Proportional,
Reset and Rate
corresponding
to P, I, and
D. These values
may be changed
once the auto
tuning is complete.
If "Disabled"
is selected,
the user will
manually enter
these three adjustment
values. If you
want the controller
to do the auto
PID and the P
, PI or PID ,
first select
auto disable
and enter 0000
for unwanted
parameter. e.q.
for PI enter
0000 for the
rate. |
|
Press ENTER
Press MAX
Press
ENTER |
*ADAPTIVE
CONTROL SUBMENU:
*(NOT INSTALLED
YET)
22) Display
flashes "Enbl"
or "dSbl".
23) Scroll
through the available
selections: Enable
or Disable.
24) Display
flashes "stored"
message and advances
to "Anti Integral"
submenu.
|
If
"Enabled", the
Adaptive Tuning
dynamically changes
and updates the
P, I, and D parameters
for optimum control.
The adaptive
tuning is useful
when the load
continuously
changes thereby
requiring new
values for P,
I, and D. |
|
Press
ENTER
Press MAX
Press ENTER |
ANTI
INTEGRAL SUBMENU:
25) Display
flashes " enbl"
or "dsbl".
26) Scroll
through the available
selections: Enable
or Disable.
27) Display
flashes "stored"
message and advances
to "Proportional
Band" submenu
if auto PID was
disabled, otherwise
it will go to
"Start PID".
|
If
"Enabled", this
feature allows
the error term
outside the proportional
band to be calculated
and accumulated
for integration.
This may be an
important feature
in applications
where fast response
time is desirable. |
|
Press
ENTER
Press MAX
Press
ENTER |
START
AUTO PID:
28) Display
flashes "enbl"
or "dsbl".
29) Scroll
through the available
selections: Enable
or Disable.
30) Display
flashes "strd"
message and advances
to the cycle
Time submenu. |
If
"Enabled",
the controller
is ready to calculate
P, PI or PID
parameters. The
set points must
be at least 20░F
or 11░C above
the (PV) process
value in order
to perform autotune,
otherwise an
error message
will be displayed. |
Note:To start auto
PlD select PID, enable
Auto PID and enable
Start PID. Sometimes
Auto PID parameter
needs fine tuning i.e.
for each 5░F over shoot
increase the Proportional
Band (PB) by 15% and
for each ▒1░F fluctuation
at the Set Point (SP)
increase reset by 20%.
Once started, do
not perform any operations
or settings before
first stopping auto-tune.
Any alarms or other
output is disabled
during auto-tune.
If
"AUTO TUNE PID"
was "DISABLED",
the display will
show the following
three submenus
so the user may
manually enter
values for Proportional,
Reset and Rate
terms corresponding
to P, I, and
D. It also can
be used for auto
PID for disabling
unwanted parameter
e. g. PI enter
0000 for rate: |
|
Press
ENTER
Press MAX & MIN
Press ENTER |
PROPORTIONAL
BAND SUBMENU:
28)
Display flashes
1st digit of
the previous
P "proportional
band" value.
29) Press
MAX and MIN buttons
to enter a new
"proportional
band" value
30) Display
flashes "strd"
message and advances
to "Reset Setup"
submenu. Note:
Proportional
band is in degree
of temperature
or counts of
process. |
|
Press
ENTER
Press MAX & MIN
Press ENTER
|
RESET
SETUP SUBMENU:
31) Display
flashes 1st digit
of the previous
I "reset" value.
32) Press
MAX and MIN buttons
to enter a new
"reset" value.
33) Display
flashes "strd"
message and advances
to "Rate Setup"
menu. Note: Reset
unit is in seconds
0-3999 |
|
Press
ENTER
Press MAX & MIN
Press ENTER |
RATE
SETUP SUBMENU:
34) Display
flashes 1st digit
of previous D
"rate" value.
35) Press
MAX and MIN buttons
to enter a new
"rate" value.
36) Display
flashes "strd"
message and advances
to the "Cycle
Time" submenu
for RTD and Thermocouple
types. If
the Output 1
is analog option
the display skips
to "Damping Factor".
Note:
Rate unit is
in seconds 000.0-399.9
|
|
Press
ENTER |
CYCLE
TIME SUBMENU:
37) Display
flashes 1st digit
of the previous
"Cycle Time"
value. |
|
Press
MAX & MIN
Press ENTER |
38)
Press MAX and
MIN buttons to
enter a new "Cycle
Time" value.
(1 to 199 seconds).
39) Display
flashes "stored"
message and advances
to "Damping Factor"
submenu.
|
Note: A cycle time
selected between 1
and 199 seconds determines
the total On/Off time
of each proportional
cycle. For example,
a 15 second cycle time
means that every 15
seconds the output
will turn on for part
or all of the cycle.
For Relay control outputs,
do not select a cycle
time of less than 7
seconds or the relays
life time will be shortened.
For a cycle time of
less than 7 seconds
select SSR or DC pulse.
Use an external SSR
with the DC pulse option
for higher currents
(higher than 1 Amp).
|
Press
ENTER |
DAMPING
FACTOR SUBMENU:
40) Display
flashes the previous
"damping factor"
selection. |
|
Press MAX
Press
ENTER |
41)
Scroll through
the available
selections: 0000,
0001, 0002, 0003,
0004, 0005, 0006,
0007, 0008 -
Default is 0003
42) Display
flashes "strd"
message and advances
to the "Output
2" menu. |
Note: Damping Factor
is a measure of speed,
overshoot, and undershoot
in which the process
variable responds to
the output changes
of the controller,
which were used during
the Auto Tune. This
value is typically
set to the ratio of
Rate to Reset. This
Default value is (0004).
For fast response time,
this value should be
decreased while for
slow response time
it should be increased.
|
Press
ENTER
|
The
"DEADBAND" submenu
will only appear
if the "ON/OFF"
was selected
from the "Control
Type" menu.
DEADBAND SUBMENU:
43) Display
flashes 1st digit
of the previous
"Deadband" value. |
|
Press MAX &
MIN
Press
ENTER |
44)
Press MAX and
MIN buttons to
enter a new "Deadband"
value
45) Display
flashes "strd"
message and advances
to the "Output
2" menu.
Note:
Dead band units
are the same
as proportional
band units. |
Note:
The Deadband or neutral
zone is the number
of degrees or counts
(if input type is process)
around the set point
which the process variable
must pass above or
below the set point,
before the output changes
state.
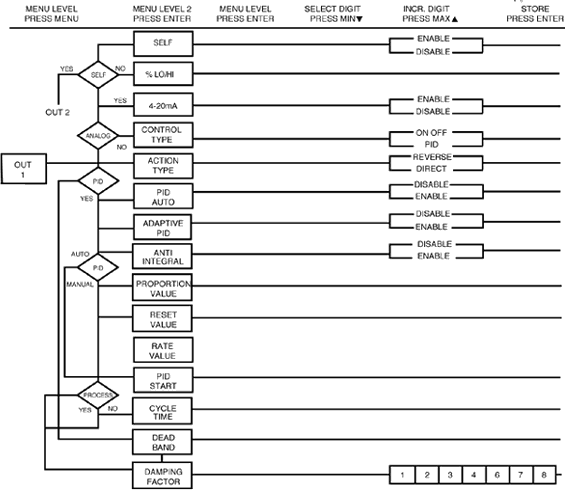
Figure
3.6 Flowchart for
Output 1
Output
2
Display
|
Action |
Response |
|
Press
MENU
Press ENTER |
1)
Press MENU, if
necessary, until
the "Out 2" prompt
appears.
2) Display
advances to "Control
Type" submenu. |
|
Press MENU
|
IF
OUTPUT 2 IS NOT
INSTALLED, THE
CONTROLLER WILL
SHOW "NOT INSTALLED"
Press MENU,
if the "not installed"
message is displayed,
advance to the
"Ramp & Soak"
submenu. |
|
Press
ENTER
Press MAX |
CONTROL
TYPE SUBMENU:
3) Display
flashes "on.
oF" or "Pid".
4) Scroll
through the available
selections: ON/OFF
or PID. |
|
Press
ENTER |
5)
Display flashes
"strd" message
and advances
to "Action Type"
submenu. |
Note:
The On/OFF control
is a coarse way of
controlling the process.
The "Dead Band" improves
the cycling associated
with the On/Off control.
The PID control is
best for processes
where the set point
is continuously changing
and/or tight control
of the process variable
is required.
|
Press
ENTER
|
ACTION
TYPE SUBMENU:
6) Display
flashes "drct"
or "rur5". |
|
Press MAX
Press
ENTER |
7)
Scroll through
the available
selections: Direct
or Reverse.
8) Display
flashes "strd"
message and advances
to "Auto PID"
submenu.
If "ON/OFF"
was selected
in the Control
Type, the display
skips to the
"Dead Band" submenu. |
Note:
The error that results
from the measurement
of the process variable
may be positive or
negative since it may
be greater or smaller
than the set point.
If a positive error
should cause the controller
output to increase
(i.e. cooling), it
would be called Direct
Acting. If a negative
error should cause
the output to decrease
(i.e. heating), it
would be called Reverse
Acting.
|
Press
ENTER
Press MAX
|
AUTO
TUNE PID SUBMENU:
9) Display
flashes "enbl"
or "dsbl".
10) Scroll
through the available
selections:
Enable or
Disable.
If "Enabled",
the PID parameter
of Output 1 will
be copied to
Output 2. |
|
Press
ENTER |
11)
Display flashes
"strd" message
and advances
to the next submenu.
|
If
"AUTO TUNE PID"
was "ENABLED",
the display skips
to the "CYCLE
TIME" submenu.
If "AUTO TUNE
PID" was "DISABLED",
the display will
show the "Proportional
Band" submenu
allowing the
user to manually
enter the Proportional
Band value.
Note:
The Reset and
Rate value are
the same as Output
1. |
|
Press
ENTER
Press MAX & MIN
Press ENTER |
PROPORTIONAL
BAND SUBMENU:
12) Display
flashes 1st digit
of the previous
"proportional
band" value.
13) Press
MAX and MIN buttons
to enter a new
"proportional
band" value
14) Display
flashes "strd"
message and advances
to the "Cycle
Time" submenu.
Note:
Refer to proportional
band. |
|
Press
ENTER
|
CYCLE
TIME SUBMENU:
15) Display
flashes 1st digit
of the previous
"Cycle Time"
value. |
|
Press
MAX & MIN
Press
ENTER |
16)
Press MAX
and MIN buttons
to enter a new
"Cycle Time"
value. (1 to
199 seconds)
17) Display
flashes "stored"
message and advances
to "Damping Factor"
submenu. |
Note:
A cycle time selected
between 1 to 199 seconds
indicates the total
On/Off time of each
proportional cycle.
For example, a 15 second
cycle time means that
every 15 seconds the
output will turn on
for part or all of
the cycle. For Relay
control outputs, do
not select a cycle
time of less than 7
seconds or the relays
life time will be shortened.
For a cycle time of
less than 7 seconds
select SSR or DC pulse.
Use an external SSR
with the DC pulse option
for higher current
(higher than 1 Amp).
The
"DEADBAND" submenu
will only appear
if the "ON/OFF"
was selected
from the "Control
Type" menu. |
|
Press
ENTER
|
DEADBAND
SUBMENU:
18) Display
flashes 1st digit
of the previous
"Deadband" value.
|
|
Press MAX &
MIN
Press
ENTER |
19)
Press MAX and
MIN buttons to
enter a new "Deadband"
value.
20) Display
flashes "stored"
message and advances
to the "Ramp
Value" menu.
Note:
Refer to proportional
band |
Note:
The Deadband is the
number of degrees or
counts around the set
point which the process
variable must pass
through before the
output changes state.
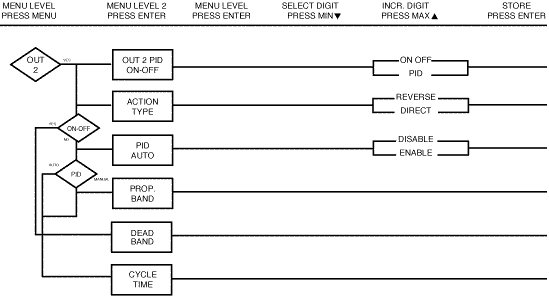
Figure
3.7 Flowchart for
Output 2
|